Britcar Trophy driver Chris Overend discusses how he has spent months perfecting the perfect at home-sim set up, based on the Team BRIT hand controls.
I’m a massive sim racing fan. I love it.
Before I joined the team, my racing was entirely online. I was obsessed with Gran Turismo as a teenager, and as an adult I was lucky enough to win a regional shootout sim racing event hosted by Aston Martin.
When my disability started to prevent my ability to race as well as I knew I could – I found Team BRIT, and everything changed in so many ways.
I was searching online for adaptive sim solutions, because after I underwent surgery for my hip dysplasia, I couldn’t brake hard enough with my left leg to race competitively. I wasn’t winning anymore and I hated it.
I got in touch with Al Locke, Team BRIT’s engineering director, who invited me over to the Dunsfold HQ. I tried out the Fanatec hand controls on the team’s Vesaro simulator, racing around Le Mans. They were incredible but I instantly had ideas about how they could be better, and could more closely replicate what we use in the cars.
I bought myself a steering wheel and hub with analog paddles on the back – the same as those in the Team BRIT workshop, and asked Al for a copy for the paddles that were in the racing car I’d be driving with the team. Al suggested I try cutting paddle shapes out of cardboard and working out the best fit for my sim set up.
That’s what I did – I took an old shoe box, drew and cut out paddle shapes, attached them to the wheel and worked out the optimum positioning for me. I then downloaded images of the hub I’d be using at home, working out different layouts and designs to get the scale and positioning right and laser cut 12 different designs.
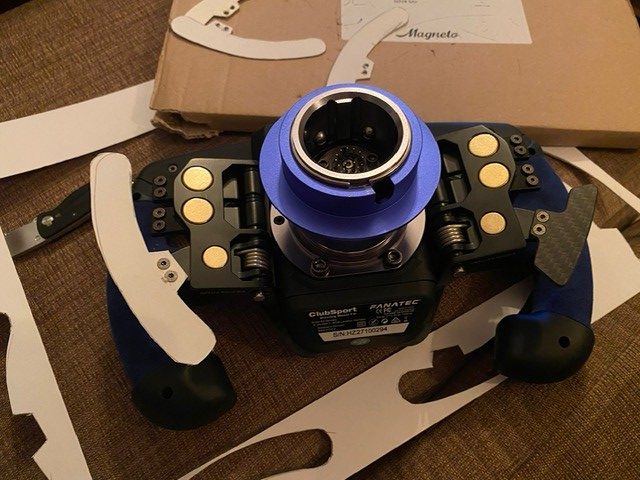
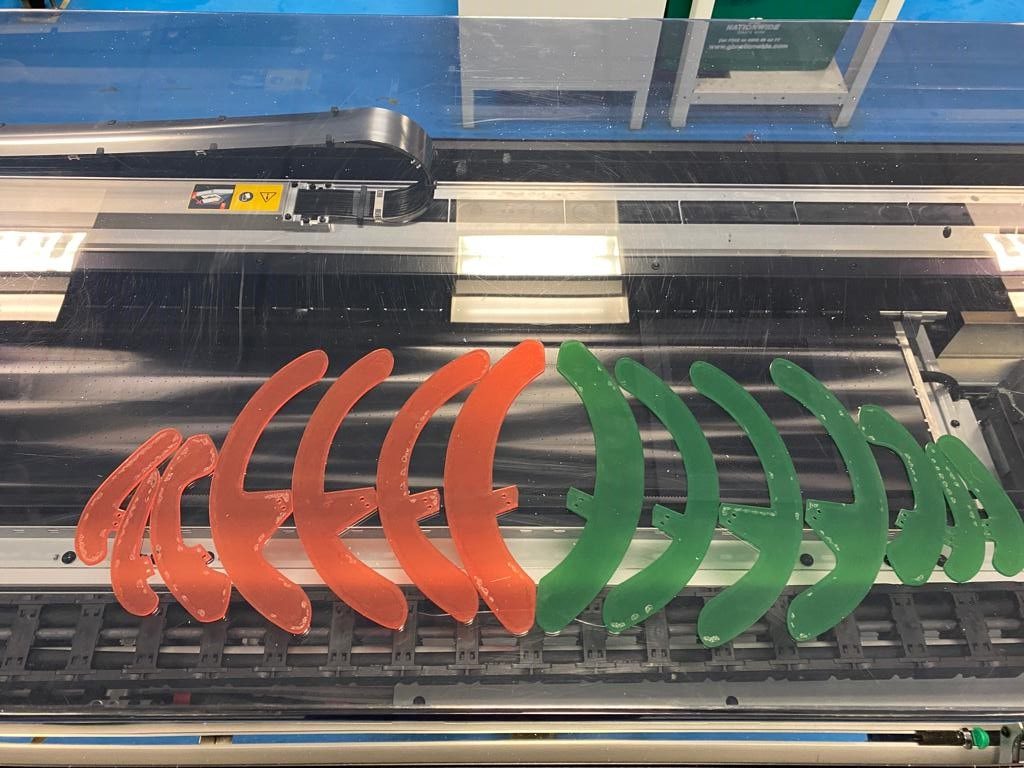
I put each of them on the wheel, made notes on which felt the best, which were too long, which were the most comfortable. I then laser cut the paddles from acrylic, but they snapped within hours of using them. Colleagues at Solent University where I teach were keen to help and gave me thicker acrylic to try. They were better, but also still snapped. Eventually I made changes to the supporting structure and finally created a solution which worked.
After a while, I realised that whilst the sim was giving me some great practice opportunities, the wheel was based on an F1 car, so wasn’t closely comparable to what I’d be driving for real. I bought a bigger rim, which was similar to the BMW rim in my Team BRIT car, but then of course the paddles I’d made were completely wrong.
I started the process all over again, laser cutting 12 different designs – which all snapped, sometimes within minutes. I then met fellow driver Paul Fullick who was keen to help with his 3d printer. He printed paddles for me which were much stronger, but I soon experienced hand pain when using them as they were too far away from my fingers. We created new ones, which surprise, surprise, also snapped, so he went away and developed some which were 20% thicker and they worked!
It’s taken so much trial and error, but we’ve created a system that works and is amazing for practicing for the real racing we’ll be doing for the team. Now, I want to further refine the design, bringing in experts from the university and from my sponsors, Dowse Engineering, to create an even better at-home solution.
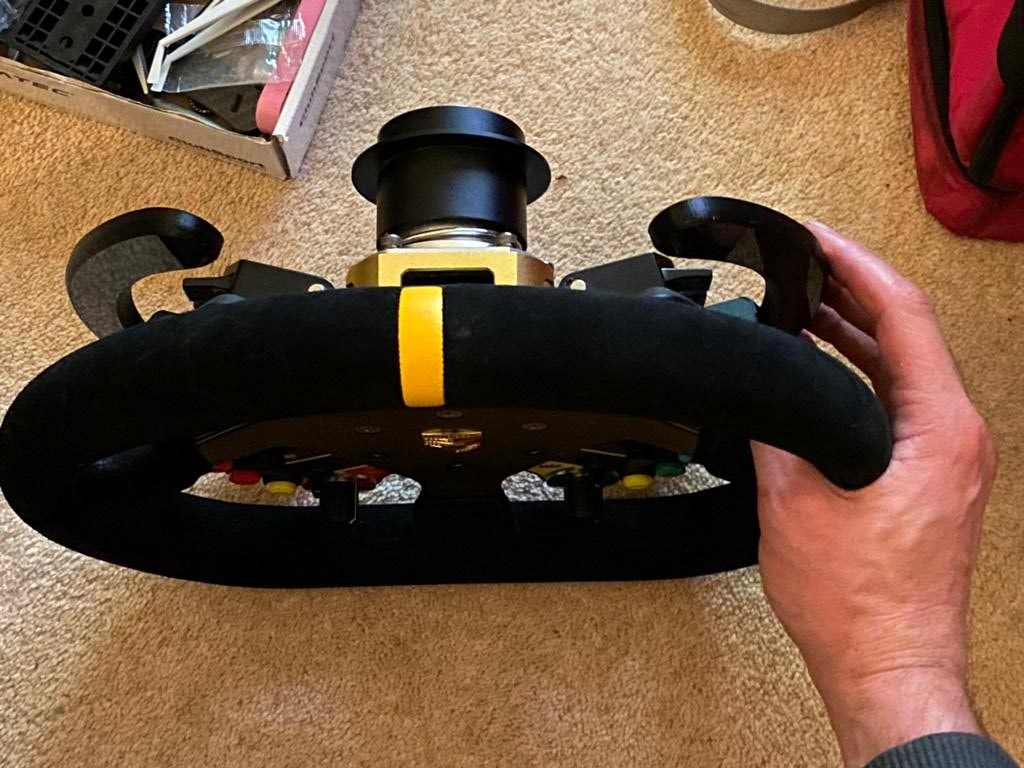
It’s been great to share all this learning with Al, who can also take some of the discovery to apply to his own engineering of the team’s hand controls. The really small differences I’ve made to my at- home set up have made a really big impact on my ability to race. Some of this, I hope, can be translated over to the development of the racing controls we have in our race cars.
The wonder of tech never ceases to amaze me, but it’s incredible what you can do when you really think about how you use something, how it feels – and then take the time to make it even better.
Chris races for team WRT in the RCCO WorldEX championship and will be competing at Spa on Tuesday 20th September. Watch the race live here.
